Graphite electrode is used as a conductive material in electric arc furnace smelting, and its consumption is proportional to the consumption of electric power. Electric Arc Furnaces are among the most important aggregates in steel production today. So, to understand a graphite electrode, first you must understand what an electric arc furnace is.
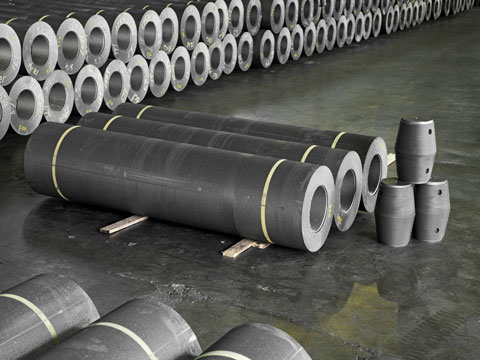
What Is An Electric Arc Furnace?
An electric arc furnace is an electric furnace that smelts ore and metal at a high temperature generated by an electrode arc. When the gas discharge forms an arc, the energy is concentrated, and the arc temperature is above 3000℃. For smelting metals, electric arc furnace has greater flexibility than other steelmaking furnaces, and can effectively remove impurities such as sulfur and phosphorus. The furnace temperature is easy to control, and the equipment has a small footprint, which is suitable for the melting of high-quality alloy steel.
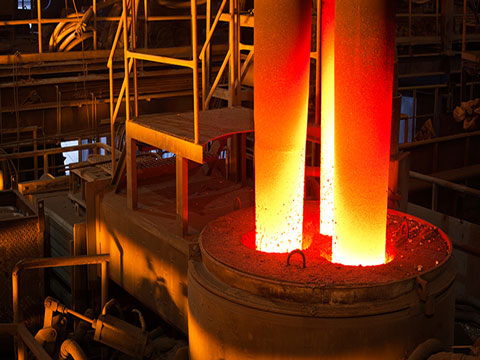
Graphite Electrode Consumption Mechanism in Electric Furnace Steelmaking Process
Graphite electrode is used as a conductive material in electric arc furnace smelting, and its consumption is proportional to the consumption of electric power. Modern electric arc furnace steelmaking uses electric energy and chemical energy as thermal energy to achieve the purpose of four (P, C, O, S), two (gas, impurity), and second (temperature, composition) in the steel making process. The performance of the graphite electrode is mainly reflected in the user whether it is applicable and consumed, and the consumption of the electrode is directly related to its own quality. The consumption of graphite electrodes in electric arc furnace smelting mainly consists of the following parts.
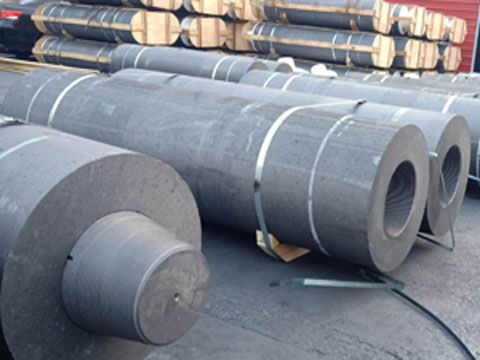
1. Consumption of graphite electrode ends and outer circular surfaces in an electric furnace
The arc generated by the graphite electrode in the electric arc furnace is divided into long, medium and short arcs, and the melting charge and the temperature rise depend on the arc power. The arc length is proportional to the secondary voltage and inversely proportional to the secondary current and the rate of temperature rise. In order to improve the smelting speed and greatly shorten the smelting time, the high chemical energy operation of forced oxygen blowing is adopted, which puts higher requirements on the oxidation resistance and thermal shock resistance of the graphite electrode.
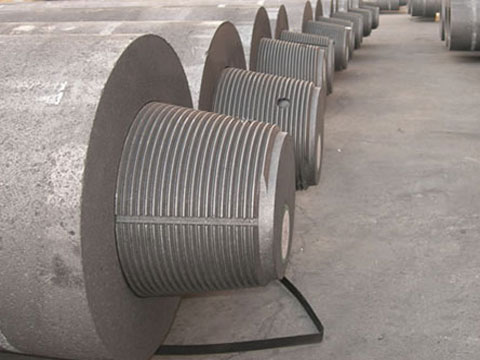
2. Residue consumption of graphite electrode produced during smelting
Residual consumption refers to the non-productive consumption part of the smelting process in which the lowermost electrode falls into the furnace and becomes the final waste. The generation of the residue is not only related to the intrinsic quality of the joint and the electrode, but also has a direct relationship with the magnetic card in the distribution of the cloth in the furnace, the atmosphere in the furnace and the operation of the power transmission.
3. The surface of the electrode is oxidized and peeled off with the consumption of opening and falling blocks.
In normal smelting production, if the surface of the graphite electrode is uneven or accompanied by flaking and falling off, there is a problem of carbonation in the molten steel.
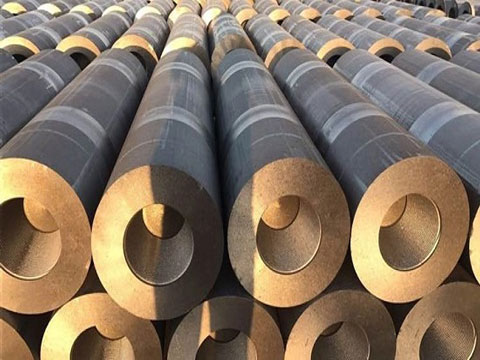
4. Direct loss caused by fracture of graphite electrode during smelting
It is a common phenomenon that graphite electrodes are broken in all electric furnace smelting, and it is also the most important factor affecting consumption. It is normal for continuous consumption and occasional breaks in a complex environment, but continuous breaks are not normal. The reason is related to many factors. The overall view can be divided into: artificial break and mechanical break. The artificial break mainly includes: bumping and scratching during lifting, improper connection or improper method, improper sliding in the flat holder, poor hardness of hard collision or transmission control.