We should understand the graphite electrode before the application to dry manic, and to check the electrode hole thread is not detailed. Graphite electrode use when air compression is used to clean the surface layer and hole threads of the spare graphite electrodes, there shall be no water or oil. Prevent cleaning with stainless steel wire or metal material brush cloth. The key is to carefully screw the joint into the electrode hole of the spare graphite electrode and screw the electrode sling (a high purity graphite sling is proposed) into the electrode hole of the other end of the spare electrode.
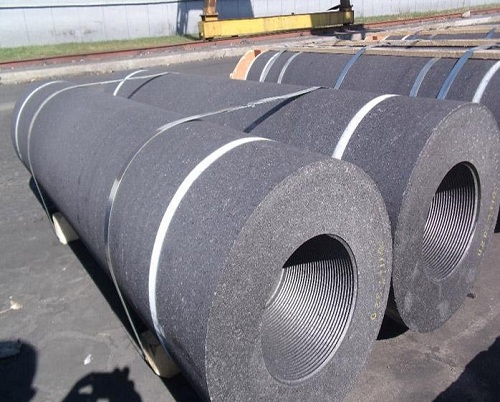
When lifting the electrode, the shock absorber rubber pad is soft to the bottom end of one end of the joint of the spare electrode component to avoid the destruction of the grounding device and the joint; The lifting hook widens to the lifting ring of the lifting device and the lifting electrode is smooth to avoid the electrode being released from the B end or colliding with other positioning devices. Secondly, the standby electrode is hoisted to the top of the electrode to be connected, pointed to the electrode hole, and then slowly fell down. Turn the spare electrode so that the screw hook and the electrode rotate down together. When the electrode finally learns to put down completely, there is no need to exert too much force, otherwise the pole hole will destroy the key points of the joint’s external threads due to strong impact. In the end, we should try our best to ensure the early solution, so as to ensure the high purity graphite in the middle and later period to produce a solid quality.
The advantages of graphite electrode use are that it is easy to process, high removal rate of discharge machining and small graphite loss. Therefore, some customers of cluster spark machine give up copper electrode and use graphite electrode instead. In addition, some special-shaped electrodes cannot be made of copper, but graphite is easier to form, and the copper electrode is heavy, which is not suitable for processing large electrodes. All these factors lead to the application of graphite electrode to some customers of group spark machines.
This series of graphite products is easy to process, and the processing speed is obviously faster than copper electrode. For example, graphite is processed by milling process, which is 2~3 times faster than other metals and does not require additional manual processing, while copper electrode requires manual grinding. Similarly, if you use a high speed graphite processing center to manufacture the electrode, it will be faster and more efficient, without the dust problem. In these processes, the choice of suitable hardness and graphite can reduce tool wear loss and copper damage. If the milling time between graphite electrodes and copper electrode is specifically compared, graphite is 67% faster than copper electrode. In general discharge machining, the machining time graphite electrode use is 58% faster than that used by copper electrode. As a result, processing time is greatly reduced and manufacturing costs are reduced.
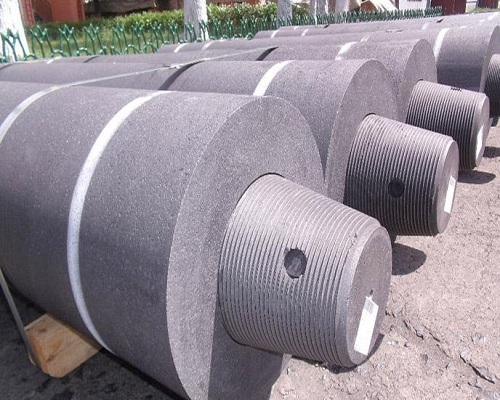
We are a professional graphite electrode manufacturer, committed to producing high-quality graphite products, complete products, reasonable price, stable and reliable quality, worthy of customer trust. Over the years, we have established friendly relations of cooperation with many customers, welcome you to come to consult procurement, we will provide you with the best quality product solutions and prices.