Application of Graphite Electrode on LF Ladle Refining Furnace
Generally, steel-making furnaces use graphite electrodes with common power and high-power graphite electrodes. Now the use of ultra-high-power graphite electrodes has increased year by year, accounting for almost half in LF graphite electrodes for steel company.
The specifications of LF graphite electrodes are generally ∮300-∮500mm. At present, the use of large-size graphite electrodes of ∮550-∮800mm is also very large, and the length of graphite electrodes is generally between 1600-2700mm.
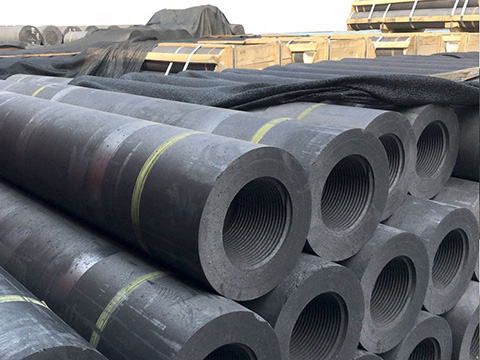
The Concept of Graphite Electrode for LF Furnace
The graphite electrode belongs to the core component of the function of the LF furnace. It converts the electric energy into heat energy to heat the molten steel. During the heating of the LF furnace, the LF graphite electrodes themselves are melted and oxidized, and the electrode is also heated and the heat is also detached, so that the molten steel is carbonized. Therefore, the quality and production process of the graphite electrode directly affects the antegrade and production cost of the LF furnace heating refining process.
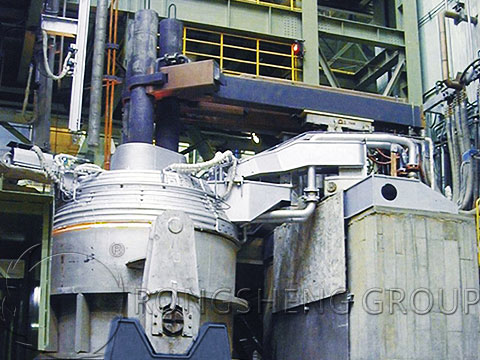
Consumption Classification of Electrodes in LF Furnace
- Electrode end face consumption
- Electrode side consumption
- Electrode breakage consumption
- Electrode stray consumption
The Reasons for the LF Furnace Breaking Electrode are:
1 When the slag is too viscous or too thin, the amount of slag is small or the bottom blowing agitation intensity is too large, the three-phase load is extremely unbalanced at the beginning of the heating arc-starting stage, so that the current density of a certain phase exceeds its load capacity, causing the electrode to break;
2 In the slag stage, if the heating gear is not properly selected, the three-phase electrode will be unbalanced and the electrode will be broken, especially when starting the arcing;
3 The electrode is of poor quality, its density is insufficient, and the current carrying capacity is low, which also causes the electrode to be broken during the heating process;
4 electrode selection is improper, the working current density is close to the upper limit of its current load capacity, the electrode often works at full load (current density), and the electrode is easy to break;
5 When the electrode is connected, the wire joint of the electrode joint is damaged, the electrode joint is irregular or not tightened, and the local current density of a part of the joint area is too large, and the electrode is broken; When the electrode is flat, the electrode (mainly the joint part) is damaged due to improper operation, and the electrode is broken during the heating process.
Additional, The reason for the LF Graphite Electrodes breakage may be that the mechanical strength of the electrode is insufficient, the electrode connection is not good, the contact resistance between the electrodes is large, the tilt of the furnace cover, the breakage of the ladle, and the molten steel crust.
Comprehensive Analysis of Factors Affecting Electrode Consumption in LF Furnace during Production
The LF graphite electrodes consumption is mainly affected by the production rhythm, the temperature rise of the LF furnace, the operation of the LF furnace, the addition of the slag-forming material, and the oxidization of the slag.
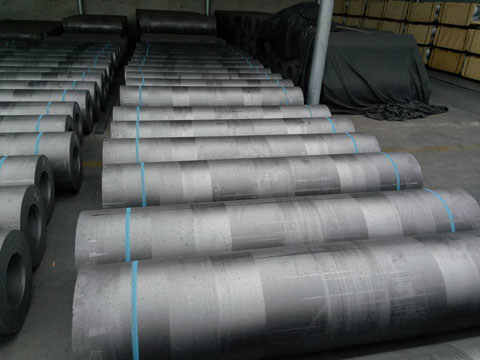
LF Graphite Electrodes Manufacturer – RS Group
RS Group is a manufacturer of LF graphite electrodes and we supply reliable graphite electrodes for LF refining furnaces. Please contact us for consultation on graphite electrodes. With lower price, faster delivery.