Graphite electrodes are critical components in various high-temperature industrial processes, particularly in electric arc furnaces (EAFs) used for steel production. These electrodes, often overlooked outside specialized industries, are essential for conducting electricity into the furnace, where it is used to generate the extreme heat required to melt steel scrap or other raw materials. In this context, the quality and specifications of graphite electrodes are of paramount importance, with Ultra-High Power (UHP) graphite electrodes being the most advanced and efficient option available. Understanding the Role of Graphite Electrodes in Modern Industry. This blog will delve into the specifics of UHP graphite electrodes, focusing on two common sizes: the 300 mm diameter and the 406 mm diameter, complete with nipples.
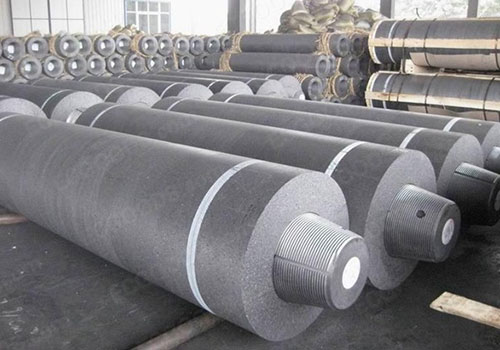
UHP Graphite Electrode 406 mm Diameter Complete with Nipple
For larger electric arc furnaces, the UHP graphite electrode with a 406 mm diameter is an ideal choice. This size is particularly suited for high-capacity operations where large quantities of steel are produced.
- Enhanced Current-Carrying Capacity
The larger diameter of the 406 mm UHP graphite electrode allows it to carry a significantly higher current than smaller electrodes. This makes it suitable for furnaces that require a higher power input to melt larger volumes of steel. The enhanced current-carrying capacity ensures that the furnace operates efficiently, reducing the time required for each production cycle.
- Nipple Configuration for Stability
The UHP graphite electrode 406 mm diameter comes complete with a nipple, which is a threaded connector that joins two electrodes together. This configuration is essential for maintaining the stability and alignment of the electrodes during operation. The nipple ensures a secure and tight connection, preventing electrical arcing between the electrodes, which can cause damage and reduce efficiency.
The use of a nipple also allows for the continuous operation of the furnace by enabling the addition of new electrodes without shutting down the process. This is particularly important in large-scale steelmaking operations where downtime can be costly.
- Longevity and Performance
Like the 300 mm version, the 406 mm diameter UHP graphite electrode is designed for durability. Its ability to withstand the harsh conditions of electric arc furnaces, including extreme temperatures and mechanical stress, ensures a long service life. This durability translates into fewer replacements, lower maintenance costs, and a more efficient steelmaking process.
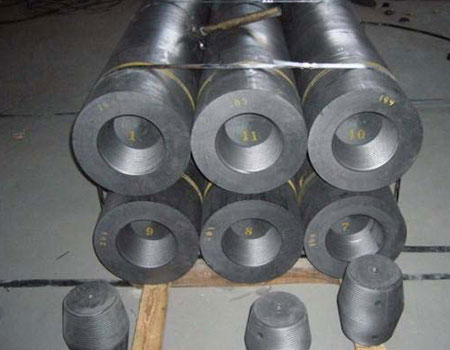
The Importance of Graphite Electrodes (DIA 8”) in Industry
Graphite electrodes come in various sizes, each suited to different types of furnaces and industrial requirements. One of the widely used sizes is the DIA 8”, which roughly translates to a diameter of around 200 mm. However, in the context of this discussion, we’ll focus on slightly larger diameters, which are more prevalent in larger and more demanding operations.
The diameter of a graphite electrode directly impacts its current-carrying capacity. Larger diameters can carry more current, making them suitable for high-power applications. The UHP grade of graphite electrodes, specifically designed for ultra-high power EAFs, offers enhanced electrical conductivity, thermal resistance, and mechanical strength compared to regular power (RP) and high power (HP) electrodes. This makes UHP graphite electrodes indispensable in modern steel production, where efficiency, durability, and performance are key.
UHP Graphite Electrode 300 mm Diameter
The UHP graphite electrode with a 300 mm diameter is a common choice for medium-sized electric arc furnaces. This size strikes a balance between operational efficiency and versatility, making it ideal for various steelmaking processes.
- High Electrical Conductivity
The UHP graphite electrode 300 mm diameter is renowned for its excellent electrical conductivity. This property is crucial because it allows the electrode to efficiently transfer the electrical energy required to create the high temperatures necessary for melting steel. The superior conductivity of UHP electrodes minimizes energy loss during the process, ensuring that the maximum amount of power is delivered to the furnace.
- Thermal Shock Resistance
Steelmaking involves rapid temperature changes, particularly when introducing cold scrap steel into a hot furnace. The UHP graphite electrode’s ability to withstand these thermal shocks is a significant advantage, reducing the risk of electrode breakage and downtime. The 300 mm diameter UHP electrode is engineered to handle these conditions, maintaining its structural integrity and performance even under intense thermal cycling.
- Durability and Cost-Efficiency
One of the key benefits of the 300 mm diameter UHP graphite electrode is its durability. The combination of high-quality materials and advanced manufacturing processes results in an electrode that lasts longer and requires less frequent replacement. This not only reduces operational costs but also enhances the overall efficiency of the steelmaking process.
High-Power Electric Arc Furnace Applications
In the realm of modern steel production, the choice of graphite electrodes can significantly impact the efficiency, cost-effectiveness, and overall success of the operation. UHP graphite electrodes, especially those with diameters of 300 mm and 406 mm, are indispensable in high-power electric arc furnace applications. Their superior electrical conductivity, thermal resistance, and durability make them the preferred choice for steelmakers seeking to optimize their production processes.
Whether you’re operating a medium-sized furnace with a 300 mm diameter UHP graphite electrode or a large-scale facility requiring a 406 mm diameter electrode complete with a nipple, these components are key to achieving consistent, high-quality results in steel production. As the industry continues to evolve, the demand for high-performance UHP graphite electrodes will only grow, underscoring their critical role in the future of steelmaking.