As is known to all, the production of graphite electrode is relatively complicated. The manufacturing process includes calcination, batching, kneading, pressing, roasting, graphitization and machining. Production time varies from process to process, up to 25 days.
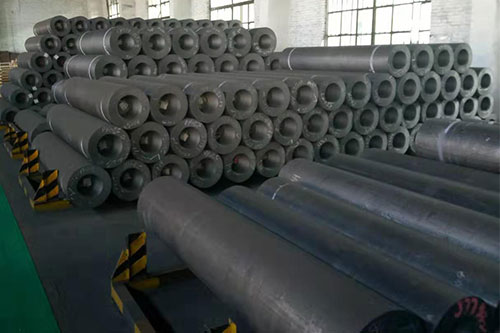
Calcination is the first heat treatment process of graphite production. The process of heat treatment of carbon materials at high temperature (1200-1500°C) under the condition of air isolation is called calcination. The structure and physicochemical properties of various carbonaceous raw materials are changed, which lays a foundation for the following process.
According to the formula requirements, the aggregate and powder of various particle size, binder respectively calculated, weighed and focused production process known as the batching. The bulk petroleum coke and needle coke must be crushed, ground and screened before batching. Kneading is the mixing and mixing of quantitative carbonaceous particles and powders with quantitative binder at a certain temperature. The process of kneading to form plastic paste is called kneading.
The essence of the extrusion process is to make the paste pass through a certain shape of the die under pressure, and then to become a certain shape and size of the hair embryo by compaction and plastic deformation. The extrusion process of the paste was carried out in the material chamber and the circular arc type for 3 days.
Secondly, it is calcination, which is the heat treatment process of the pressed product in the protective medium in the heating furnace under the condition of isolating air and heating at a certain rate. It is one of the main processes in the production of carbon products and an important link in the three heat treatment processes in the production of graphite electrode. The roasting production cycle is long (22-30 days) and the energy consumption is high.
Impregnation is a process in which the carbon material is placed in a pressure vessel and the liquid impregnating agent bitumen is immersed into the pores of the electrode of the product at a certain temperature and pressure. The immersion time is generally four days, the purpose is to reduce the porosity of the product, improve the density, increase the compressive strength, reduce the resistivity of the finished product, and change the physical and chemical properties of the product.
The secondary roasting is the process of carbonizing the asphalt immersed in the pores of the calcined product. The electrode and the joint blank with high volume density need to be baked twice (15 days), and the joint blank needs to be soaked and baked many times.There is graphitization, graphitization refers to the high-temperature heat treatment process in which the carbon products are heated to more than 2300 C in the protection medium in the high-temperature electric furnace, so that the amorphous random layer structure of carbon is transformed into three-dimensional ordered stone and ink crystal structure with graphite structure. It will take 15 days.
The last step is machining. Machining is the process of making electrode body and joint in accordance with the requirements by means of machining to reach the required size, shape, accuracy, etc.
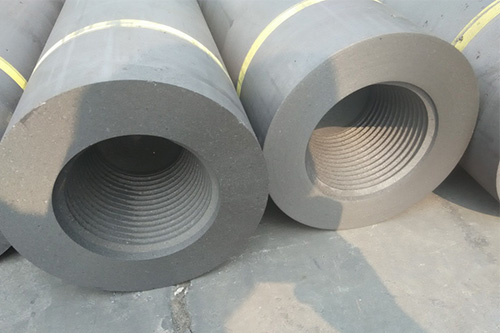
The production process of graphite electrode is relatively complicated, with a long production cycle. The production time of ordinary graphite electrode is more than 50 days, and the production time of ultra-high power electrode is up to 65 days. As a consumable material, the potential of graphite electrode in the market is very strong.